Custom Printing
Plastic Cup Printing Process
In the realm of Plastic Cup Printing Processes, a variety of techniques come into play, including silk screen printing, pad printing, and thermal transfer printing. The selection of the ideal printing method hinges on factors like the material of the product, its surface characteristics, cost considerations, the desired pattern effect, pattern adhesion, and authentication prerequisites. Making a thoughtful choice in the Plastic Cup Printing Process is pivotal to ensuring the attainment of the desired outcome.
Silk Screening on Plastic Cup
"In the realm of Plastic Cup Printing, our automated silk-screening machine excels in curved screen printing, accommodating a wide range of shapes such as cylinders, ovals, and flats crafted from plastic, glass, metal, and more. Our printed plastic product portfolio includes plastic water bottles, cups,and similar items.
The Plastic Cup Printing process provides the versatility to utilize customized colors and achieve an array of surface effects using specialized inks. This method delivers vibrant, bold, durable, and metallic colors that ensure logos and images command attention and prominence."
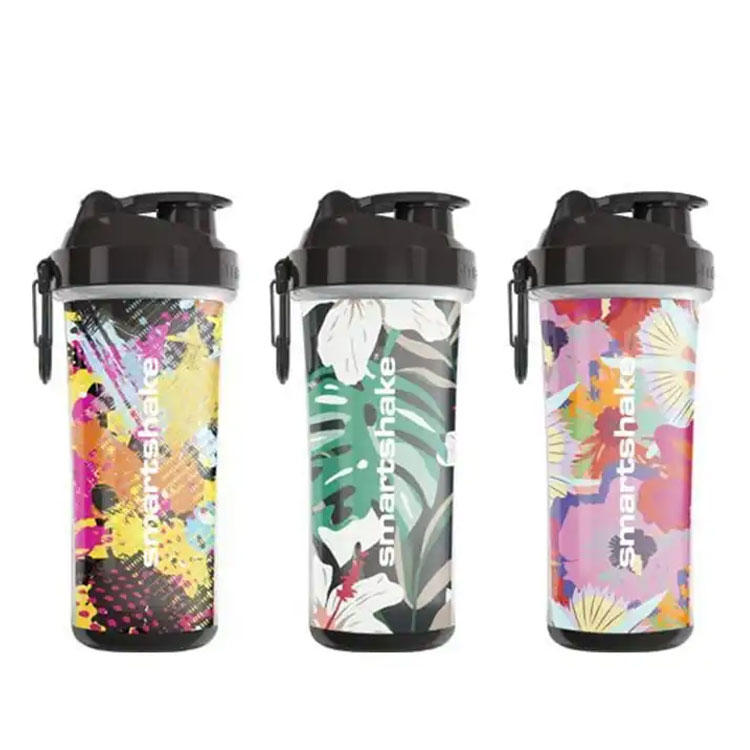
Features of Silk-Screening on Plastic
- Silk-screened images and logos boast vibrant and enduring colors, resistant to fading, tearing, staining, wrinkling, or peeling off.
- The imprints on bottles or cups remain intact even when exposed to water.
- Silk-screening is a cost-effective method.
- Permissible plastic materials for this process include polypropylene, polyester, polyethylene, polycarbonate, and acrylic.
- Screen printing allows for efficient mass production and swift delivery of large batches.
Heat Transfer Printing on Plastic
Heat transfer printing, also known as thermal transfer printing, is a popular method for imprinting designs onto plastic cups and bottles. It's widely employed to transfer logos and images effectively onto these plastic surfaces.
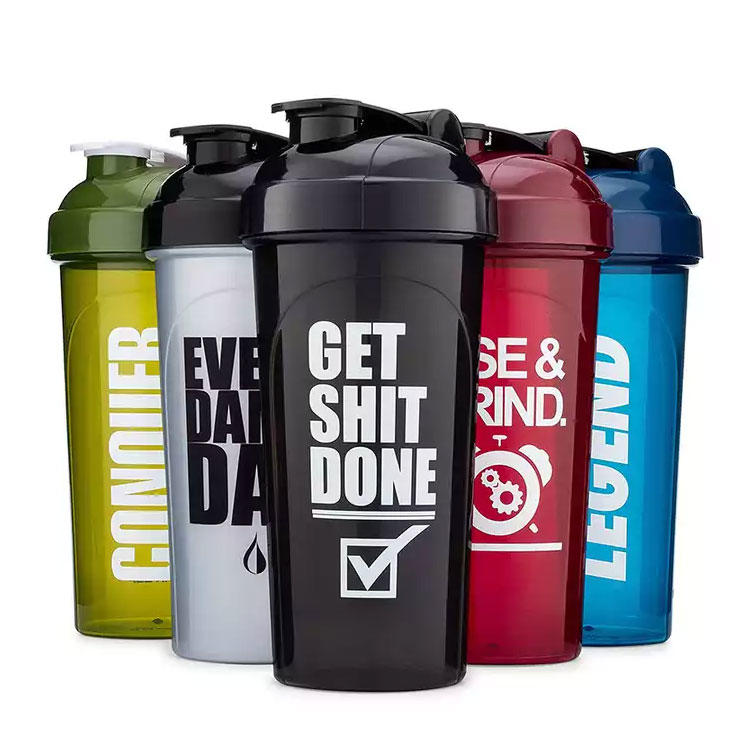
Features of Heat Transfer Printing
- Heat transfer printing boasts the ability to create high-quality, photo-realistic, and vibrant images.
- The resulting image remains enduring and does not fade over time.
- The transferred image on mugs or other objects won't wash off when exposed to water.
Pad Printing on Plastic
Pad printing involves blending a solvent-based pad printing ink with solvents, hardeners, and other chemicals. Different substrates require specific inks for printing. Utilizing a pad printing machine, ink is placed into an ink cup and positioned on the machine’s pad. An etched plate serves as a stamp in the pad printing machine, transferring the artwork from the pad onto the product.
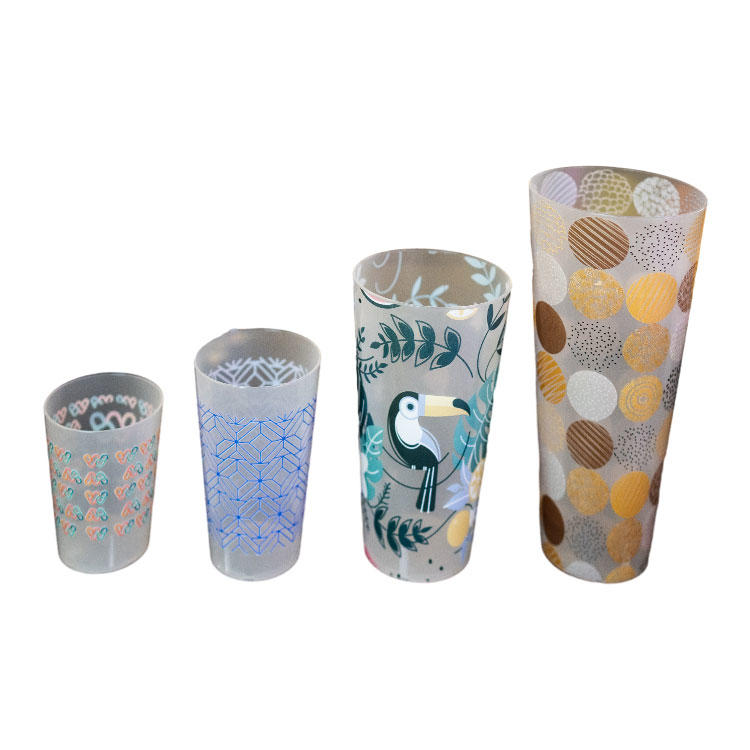
Features of Pad Printing on Plastic
- Pad printing allows for the creation of 1-to-6-color images with precision.
- It offers a cost-effective printing solution.
- Ideal for printing on bottle caps of varying shapes and sizes.
- Offers easy adaptability to different bottle cap varieties and entails a straightforward plate-making process.
UV Printing on Plastic
UV printing, a direct-to-substrate technology, utilizes UV ink jet printing. Artwork is created in design software like Photoshop or Illustrator, then sent to the printer. The printer uses cyan, magenta, yellow, and black ink to produce the design as small droplets on the product. UV/LED light cures the ink. Both one-color and three-color printing machines cater to different needs. UV silk screen printing machines efficiently print a large quantity of bottles per minute with perfect color-to-color reproduction. It's versatile for printing on various plastic cup and bottle shapes—round, oval, and square.

Features of UV Printing on Plastic
- UV automated screen printing machines achieve a high throughput of 4000+ bottles per hour.
- Capable of printing logos on plastic bottles of diverse shapes.
- Automated operations ensure stability and precision throughout the printing process.
- A versatile, all-in-one machine streamlines and enhances the printing process.
- Efficient and eco-friendly with low energy consumption.
Plastic Electroplating Process
Electroplating is a method where an electrical current is employed to deposit a thin layer of metal onto plastic surfaces. Primarily used to impart a luxurious finish and specific properties to plastic items, such as anti-corrosion, anti-rust, increased wear resistance, and improved appearance.
Features of Plastic Electroplating Party Balls
- Elevates the overall look with a bright and luxurious appearance, ideal for diverse party settings.
- Enhances durability through the application of a metallic outer surface.
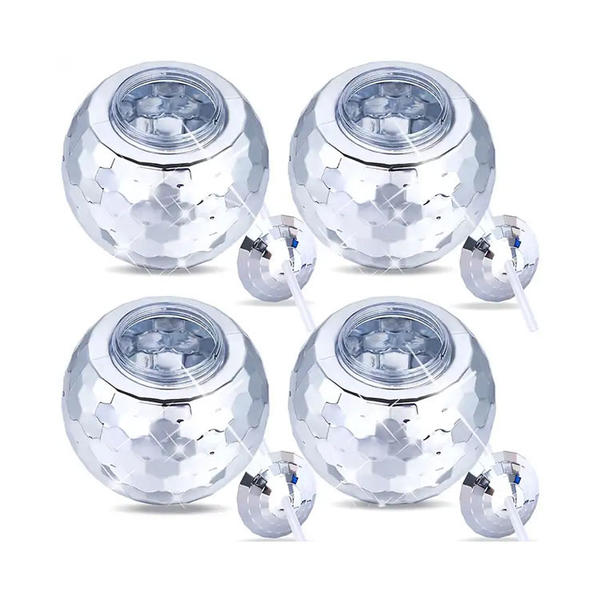
Plastic Painting Process
Spray painting is a prevalent surface treatment method, particularly for plastics like nylon, PP, ABS, and PC. ABS and PC usually exhibit good adhesion for paints. Various paint options are available, such as ordinary paint, rubber paint, PU paint, UV paint, and more. Fully automated spraying ensures a consistently uniform coat across the product's surface.

Custom Design

Plastic Moldings
